Security System Installation Checklist for Sioux Falls Warehouses
An owner’s guide to protecting inventory, uptime, and peace of mind
On this blog you will learn:
- How to plan, budget, and phase a warehouse security system—from threat mapping to hardware selection.
- Best-practice tips for integrating CCTV, alarms, access control, and 24/7 monitoring into one automated security system workflow.
- Maintenance, compliance, and staff-training steps that turn equipment into long-term risk reduction.
Warehouses and distribution centers face a unique mix of risks: open dock doors, tall pallet stacks that hide movement, and long overnight hours. The checklist below walks you through every critical step—from defining threats to training staff—so you can build
integrated security systems that fit your budget and meet Sioux Falls compliance requirements for warehouses.
1. Map Your Threat Profile
Create a simple two-column chart:
threat and
potential impact. Include external risks (cargo theft, perimeter breaches), internal risks (employee shrink), and environmental risks (fire, flooding, power loss). Beside each, write the estimated dollar loss or downtime a single incident would cause. High-impact threats deserve priority funding in your
security system installation plan.
2. Set the Budget & Phasing Strategy
Security projects rarely happen in one sweep. A realistic plan allocates:
- Phase 1 – Foundation: Perimeter cameras, intrusion alarms, door contacts.
- Phase 2 – Enhancements: PTZ cameras for aisles, analytics for vehicle or badge tracking.
- Phase 3 – Expansion: Environmental sensors, asset-tracking beacons, AI analytics.
Aim for 60 % hardware, 25 % labor, 15 % ongoing support. Phasing lets finance teams approve smaller tranches while moving steadily toward
24/7 security monitoring
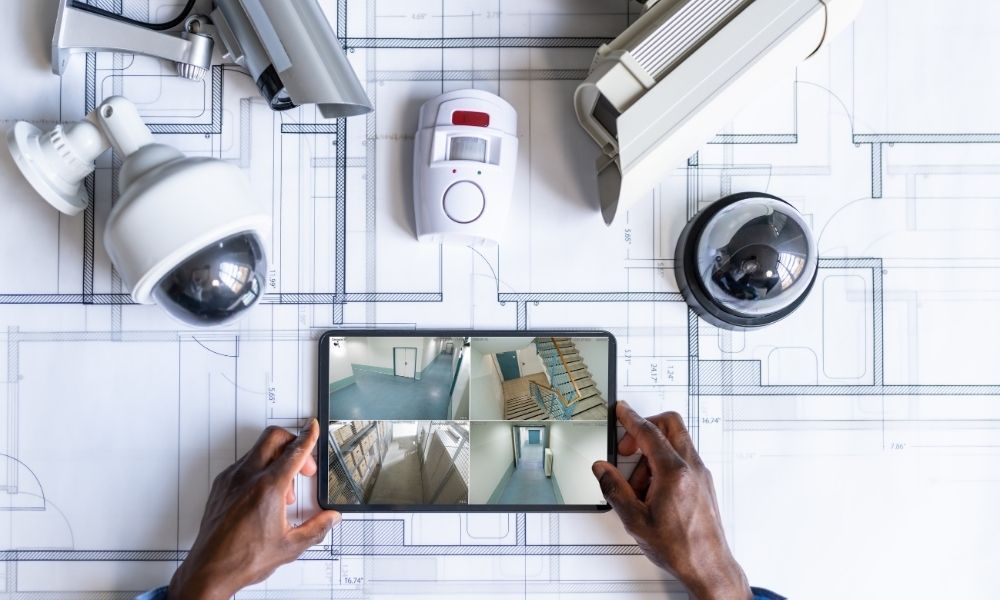
3. Conduct an On-Site Risk Walk
Grab a floor plan, laser measurer, and Lux meter. Walk every dock bay, mezzanine, and rack aisle, noting:
Checkpoint
Light levels
Wi-Fi signal
Line-of-sight
Notes to capture
IR cameras need < 700 lux or IR illumination
Mesh or wired drops for metal-shelving dead zones
Ensure cameras clear 12 ft rack tops
This documentation prevents blind spots and guides camera placement for effective
CCTV installation. Photograph tricky areas; photos help during vendor quotes or internal presentations.
4. Choose Hardware Wisely
Choosing the right equipment can greatly increase the effectiveness of your warehouse security system. Below, we have curated a list of 4 things to keep in mind when building a security system for your warehouse.
Cameras – NDAA-compliant 4 MP turrets at docks, 360° PTZ units for aisles, IR bullets for perimeter fences.
Intrusion sensors – Glass-break detectors on office windows, motion beams on dock doors.
Access control – Cloud-managed badge readers with mobile credential support and automatic badge expiry for temps.
Environmental – Heat/smoke detectors above packaging areas, water sensors near sump pits.
Match resolution, frame rate, and storage days to your threat profile. Cross-compatibility among devices reduces integration headaches and keeps
alarm monitoring unified in one dashboard.
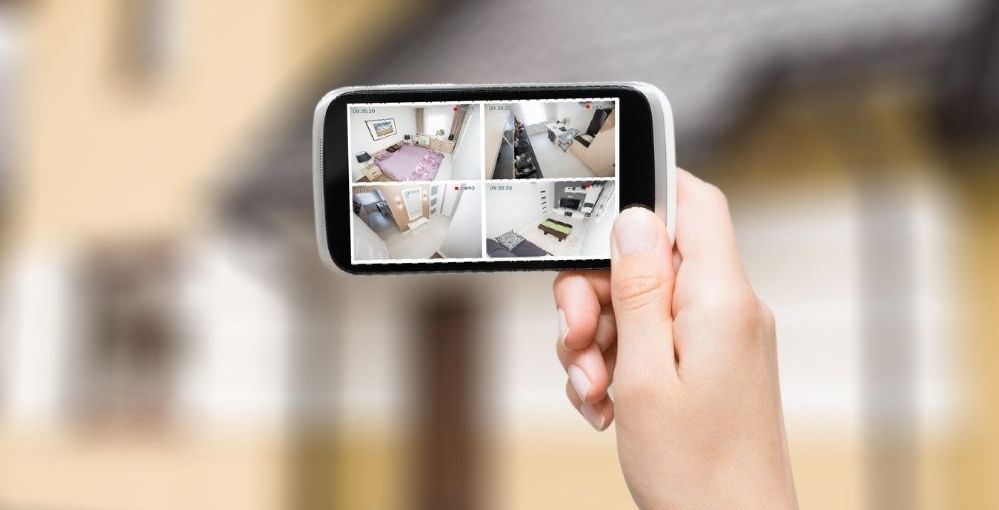
5. Integrate & Automate
True security emerges when systems talk to each other:
- Alarm triggers push 20-second camera clips to supervisors’ phones.
- After-hours badge rejection escalates to text and email within 30 seconds.
- Dock doors left open > 3 minutes flash a strobe and start recording.
Use simple IFTTT-style rules in your VMS or access-control software. Integration transforms hardware dollars into
business security systems that deter, detect, and verify in real time.
6. Align With Compliance & Insurance
OSHA requires at least 5 foot-candles of illumination in active aisles; NFPA 731 outlines intrusion-detection practices for commercial properties like warehouses. Meeting or exceeding these standards not only avoids citations but can also trim 5–15 % from insurance premiums. Document all camera views, retention periods, and monitoring certificates—you might need them during an audit or claim.
7. Train Staff & Establish SOPs
Technology fails if no one knows how to use it. Develop a 30-minute orientation covering:
- How to bookmark and export video clips.
- Steps to acknowledge and reset intrusion alarms.
- Daily checks for camera obstruction or tampering.
Laminate quick-start cards and post them at guard shacks or supervisor desks. A trained team turns equipment into reliable warehouse security system.
8. Plan Maintenance & Upgrades
Set recurring reminders for firmware updates, lens cleaning, and sensor battery checks. Keep spare cameras and door contacts on-site to minimize downtime. Review footage monthly; patterns of near-misses often reveal workflow tweaks that cost less than new hardware. If DIY maintenance feels daunting, schedule an annual audit by certified
security system installers to catch issues early.
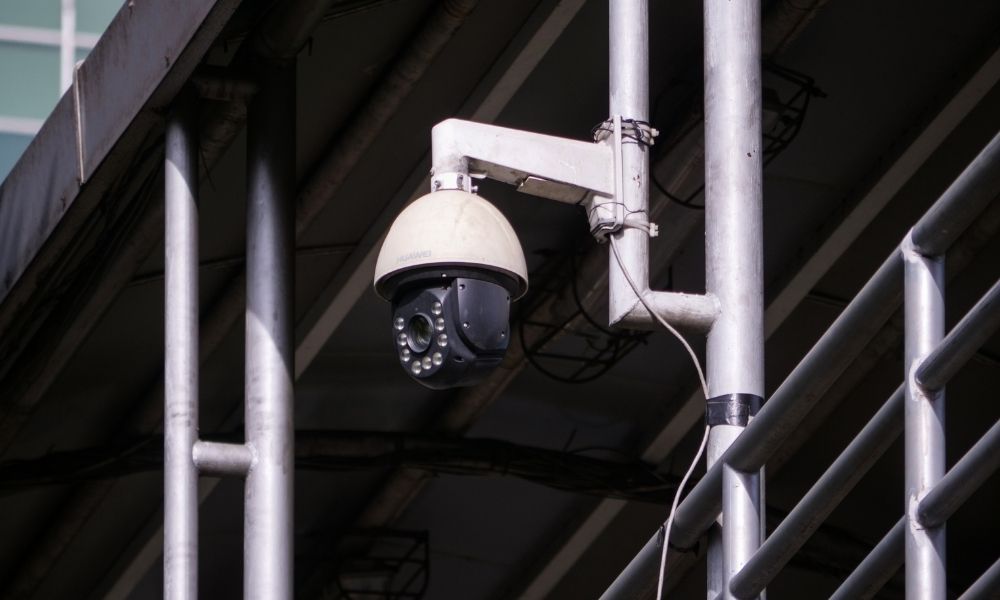
Key Benefits Recap
- Reduced shrinkage: Visible cameras and badge logs deter theft.
- Faster response: Integrated alerts shave minutes off incident timelines.
- Lower premiums: Documented monitoring can cut insurance costs.
- Compliance peace-of-mind: Systems aligned with OSHA & NFPA avoid fines.
- Operational insight: Analytics reveal inefficiencies beyond security.
What now?
Prefer a professional review before you buy hardware?
24/7 security monitoring specialists in Sioux Falls are a phone call away at 605-334-9357—no pressure, just straight answers.
FAQ
1. What are the essential components of a warehouse security system?
A balanced setup includes perimeter and interior cameras (turret, PTZ, IR bullets), intrusion sensors on doors and windows, cloud-managed access-control readers, environmental detectors (smoke, water), and a central video-management/alert platform.
2. How many cameras does a typical 10,000-sq-ft warehouse need?
Plan for one wide-angle camera per 2,000 sq ft indoors plus dedicated units for each dock door and exterior corner. A 10,000 sq ft building usually requires 8–10 cameras for full coverage.
3. What’s the difference between motion detection and video analytics?
Motion detection triggers on any movement, which can lead to false alarms; video analytics uses AI to classify people, vehicles, or specific behaviors (loitering, line-crossing) for more precise alerts.
4. How long should security footage be stored?
Most insurers and regulatory bodies recommend 30 days of retention; high-risk industries (pharma, food) may keep 90 days or more for audit trails.
5. How often should sensors and cameras be inspected or serviced?
Perform visual checks monthly, clean lenses quarterly, and run full firmware updates at least twice a year. Critical sensors (door contacts, smoke) should be tested every six months.
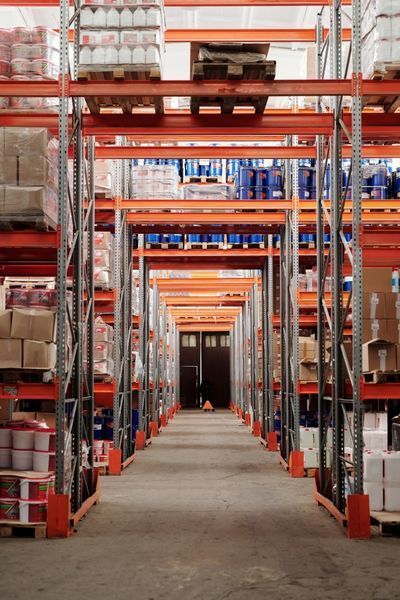